Private, Public, or Contract: Which Warehousing Type is Right for You?
Searching for storage space can be challenging, because uncertainty can cloud judgment. With so many types of warehousing such as private, public, and contract warehousing, finding what’s right is like looking for a needle in a haystack. It’s important to understand which model aligns best with your operational needs and growth strategy. Follow along to learn about each type of warehousing and how to choose the right fit for your business.
Consider Facility Features First
Before selecting a warehouse to store and manage inventory, it’s important to step back and prioritize short- and long-term business goals. Finding the right space takes evaluating today’s needs and planning for tomorrows. Why?
Just as strategic planning shapes product development and business growth, choosing the right warehousing option requires foresight. It should align with current needs while allowing for future expansion. Although product industry, use, and customer audiences will differ, these storage fundamentals serve as a guideline to keep decision-making in check.
Location, Location, Location
One of the easiest ways to experience cost savings is by storing product in a warehouse close to major transportation routes, suppliers, and customers. By operating near ports, railways, and highways, logistics are streamlined and transit times reduced. For example, a Midwest warehouse in Chicago enables 2-day shipping to nearly 70% of the U.S. population.
Warehouse Size & Scalability: Why Bigger Isn’t Always Better
Finding the right warehouse choice has a lot to do with the building footprint and whether it has the ability to scale when business expands. Your warehouse should accommodate future expansion—both in physical space and operational capacity Depending on the type of products involved, building height and floor load capacity can also impact space utilization and efficiency.
Revealing Warehouse Cost
Operational and financial due diligence done sooner than later is worth the extra effort and can eliminate undue stress. Preparing a cost breakdown that includes rent or purchase price, utilities, taxes, maintenance expenses, potential upgrades needed, and other operating expenses helps avoid operational sticker shock down the road. Move through the process, avoid analysis paralysis, and rely on what the numbers show. Either the warehouse fits in the budget or it’s onto the next…
How Technology is Transforming Warehousing
Modern warehouses are equipped with advanced technologies that increase visibility and transparency across the facility but also connect workers and systems into a seamless operational approach increasing efficiency, safety, and accuracy while reducing costs. This level of automation comes in many forms. ASRS (automated storage and retrieval systems) include robotics or computer technologies that help retrieve and store inventory. WMS (warehouse management systems) can track product location from pallet to picking, packing, boxing, loading and distribution.
Regulatory Compliance
If your business handles hazardous materials (HAZMAT), choosing the right warehouse is essential for safety and compliance. Not all facilities meet OSHA, EPA, DOT, and NFPA regulations, which require proper containment, fire suppression, and ventilation systems. HAZMAT warehouses should have certified personnel trained in OSHA HazMat handling, HAZWOPER, and DOT regulations to ensure safe storage and transport. Before leasing or purchasing, businesses must research local zoning laws, environmental standards, and permitting requirements to confirm compliance. Verifying these factors in advance helps avoid safety risks, regulatory fines, and supply chain disruptions.
Scalability & Flexibility
A lot can happen over the course of operating a business, which is why a warehouse works best when it’s flexible enough to meet evolving needs. Look for a facility conducive to easy expansion or reconfiguration to align with increasing activity.
But flexibility may not be enough. To effectively scale business, strategic shifts alongside operational ones build strength across multiple departments, assisting product development, sales, and marketing in quick responses to changing environments. This agility is especially important in warehousing and transportation when disruptions happen, and why solutions can be planned for well in advance.
Active Risk Mitigation
Protecting business is more than safeguarding people, products, and storage premises; it’s securing a positive future. Inventory storage and handling of products come with risks, some known and others unknown. Ask warehouse owners about their current security measures and if surveillance cameras, access control systems, and fire suppression systems are in place. Safe working environments also keep operations OSHA-compliant, so check for adequate lighting, ventilation, and ergonomic design too.
With this list of considerations deciding on the right storage choice is that much closer. Here below are specific warehousing types and the characteristics that set each apart.

Public or On-Demand Warehousing
Public warehouses are an attractive choice for many companies because it provides an all-inclusive services package. A third party manages the warehouse, allowing manufacturers, suppliers, and retailers to rent storage space for their raw materials or products. But there’s more to public warehousing than just storage.
Warehouse managers take inventory control, packaging, and order fulfillment off the tenant’s hands and treat stored products as if they were their own. The warehouse can be rented under a short-term lease or a multi-year agreement, ideal for businesses needing storage solutions to accommodate seasonal demand surges or for interim storage between long hauls.
Private or Dedicated Warehouses
Not quite ready to let go of the fulfillment and logistics reins? There’s a storage option for that too—private warehousing. For businesses wanting to own operations from the ground up keep business dealings close to the vest, and manage inventory independently, private warehousing is a tailor-made choice.
Companies with specialized products or longstanding systems in place can quickly adjust in these owner-operated spaces without having to reinvent the wheel. And when new product lines are introduced or orders increase, businesses have the flexibility to reconfigure storage, order fulfillment, packaging, and logistics processes to meet evolving scale, without needing outside approval.
But the responsibility of operations remains with the business owner, which is okay if day-to-day control over warehousing and inventory defines their comfort zone. However, conducting a cost vs. benefit analysis can help dispel misunderstandings about the value of private warehousing, industrial property ownership, and the added expenses.
Contract Warehousing
Wanting a logistics solution offering a happy medium between public and private storage? Contract warehousing provides the best of both worlds.
Like other industrial warehouse leases, a contract warehouse agreement involves the building owner and a tenant who rents space. What goes on inside the facility is disclosed in the contract: the types of materials and products stored, specific regulatory requirements affecting operations, hours of operation, and other terms of the lease. But the day-to-day business operations are the sole responsibility of the tenant.
Costs related to materials, equipment, and onsite workers, as well as investments in technology and automation are made and managed by the tenant. The big takeaway benefit of contract warehousing is it gives a business freedom to run their operations without being under the microscope of a third-party operator.
The flexibility of contract warehousing goes further and delves into negotiating terms based on anticipated use and identifying spatial needs.
Shared Contract Warehousing
Businesses with inconsistent storage needs, like those dealing with seasonal inventory spikes, appreciate the practicality shared contract warehousing offers. With it, the storage building is split amongst several different customers, where their individual rent is based on the square footage used. It’s a bare-bones warehousing option and can prove ideal for startups too.
Dedicated Contract Warehousing
If more customization and specialization are needed, a dedicated contract can be drafted to cover specific tenant requirements. For both building owner and business operator, dedicated contract warehousing means more conversations between the parties before the lease begins, eliminating surprises and setting expectations early on. Because pricing is predetermined and fixed, warehouse costs are predictable giving a solo tenant one less thing to worry about.

Warehouses Designed for Product Types
Whatever materials, components, or finished products support a given business, some may need special attention that a standard warehouse facility can’t provide. For those scenarios, it’s important to devote extra time to ask a storage building owner more detailed questions about the space and how much leverage there is to ensure the right fit.
Climate-Controlled Storage
Not all warehouses will meet every business’ needs. Sensitive products like medicines, cosmetics, and food products require storage and handling in the right temperature settings. Without it, product integrity is lost, leading to costly and potentially harmful consequences. Companies responsible for these kinds of products are best served by warehouses that offer the ability to increase shelf-life through climate-controlled space. But expect the increased energy use to raise storage costs.
HazMat Storage
Hazardous materials and chemical substances need extra care during handling, stocking, and storing. To save on time, keep warehousing choices to HAZMAT warehouses only. Though they are like a climate-controlled warehouse in that both follow specific safety standards, HAZMAT-dedicated warehousing bears stronger requirements.
Building owners, operators, and workers involved in the storage, handling, and loading of hazardous materials must maintain government-mandated safety, health, and protective measures. These specialized facilities often come with skilled workers trained and certified for HAZMAT duties. And with the 24/7 security systems and/or staff in place, storing chemicals can be costly, but worth the investment toward security and peace of mind.
Foreign Trade Zone (FTZ) Warehouses
When importing products internationally, customs officers inspect each shipment to certify their entry into the country. Bonded or foreign trade zone (FTZ) warehouses, located near borders, airports, or port cities, serve a specific purpose: to store, load or unload products coming into or going out of the U.S.
FTZ warehouses allow product receivers to store goods but are obligated to pay duties owed once products officially enter the U.S. for consumption. In contrast, bonded warehouses allow importers to store goods without paying tariff duties until the products are sold or released from the warehouse. And with international trade and geopolitical climates in constant flux, knowing what’s expected at the border can keep product shipments moving.
How to Choose the Right Warehousing Option
Finding the right warehouse space takes more than walking a property, reviewing the numbers, and fine-tuning the contract terms. It’s about knowing how to absorb information, apply it to business forecasting, and defining a pliable and fixed solution. Finding the right storage facility goes beyond inventory solutions—it meets efficiency at scale onsite and in contract.

About the Author
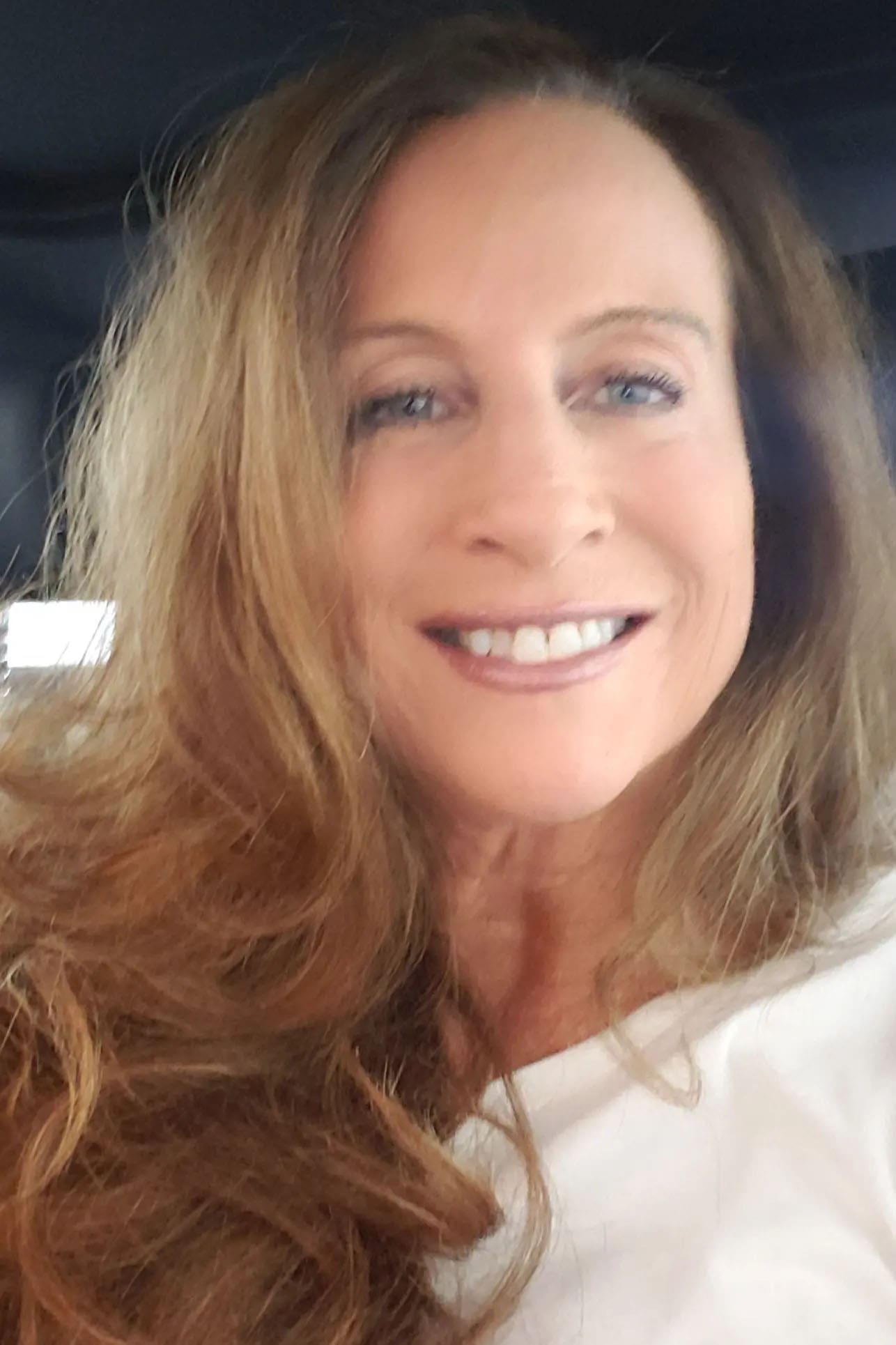
Melanie Stern
Melanie enjoys a longstanding career in communications, crafting content for varied industries. Her experience includes writing blogs, news editorial, feature articles, social, and broadcast segments. She also hosts Institute for Supply Management’s bi-weekly podcast “Supply Chain – Unfiltered”.