How a top plastics producer optimized warehousing & distribution
Managing Complex Chemical Logistics
Download the PDF
In the chemical space, warehousing, handling, and shipping is a complex and delicate task. It requires the right expertise and significant resources, which is why many companies turn to 3rd party logistics providers for support. But warehousing and transportation of hazardous materials can’t be run by just any 3PL. Between strict safety and sustainability compliance requirements and highly specialized operational equipment and training, finding a solid 3PL partner becomes crucial.
In this case study, we will explore how a top plastics producer in the United States successfully managed complex chemical logistics with the support of WSI. The partnership has grown over several years with a mix of multi-tenant warehousing and dedicated facility operations.
A Partnership Built on Trust and Expertise
This customer is a leading producer of advanced polymers and high-performance plastics with a rich history dating back to the 1860s. Their vision is to pioneer a circular economy that reduces waste, extends the usefulness of commercial products, and sources eco-friendly raw materials.
Their products are used in various applications, including automotive components, electronics, medical equipment, renewable energy systems, and construction materials.
As a global leader in their field, this plastics distributor has consistently pushed the boundaries of material science to create innovative solutions for a wide range of industries. The ideal 3PL partner would need to provide tailored solutions and share the company’s commitment to excellence and corporate responsibility.
WSI’s journey with this customer began in the early 2000s when they sought a solution to their initial logistics challenges:
- Operational inefficiencies
- Inflated storage and handling rates
- Alarming rate of shipping errors
Through a long-standing partnership with WSI, the top plastics producer has achieved significant improvements in operational efficiency, reduced costs, and enhanced customer satisfaction. With a strong foundation of trust and shared values, the partnership continues to thrive
The Tailored 3PL Solution
Chemical Warehousing Industry Leaders
This plastics producer had many complex needs, including specialized expertise in managing a highly regulated tank farm. Staffing, training, and leading an operation of this nature demands a deep understanding of regulatory compliance, safety protocols, and operational expertise. WSI’s team of subject matter experts, including a seasoned Director of Chemical Operations and a full support staff, delivered comprehensive solutions to meet these needs. This leader actively participates in the customer’s functions and training events to better understand their operational standards.
Customizing Warehouse Operations
The ideal solution for this customer required services across multiple sites. WSI’s flexible services allowed them to optimize their existing facilities while reaping the benefits of the 3rd party network of warehouses and experts. This hybrid approach enables companies to maintain ownership of their assets while outsourcing day-to-day operations and logistics expertise. Customers at both dedicated and multi-tenant facilities can benefit from WSI’s scale and experience.
In addition to warehousing expertise and value-added services, WSI’s team provides IT support, human resources, and a rigorous training program. We have HAZWOPER, IMDG, IATA, & DOT as well to manage chemicals safely, from inbound logistics to distribution. WSI has also made investments in expanding temperature-controlled storage, flammables storage, and tank farm management to demonstrate its commitment to supporting customers’ diverse needs.
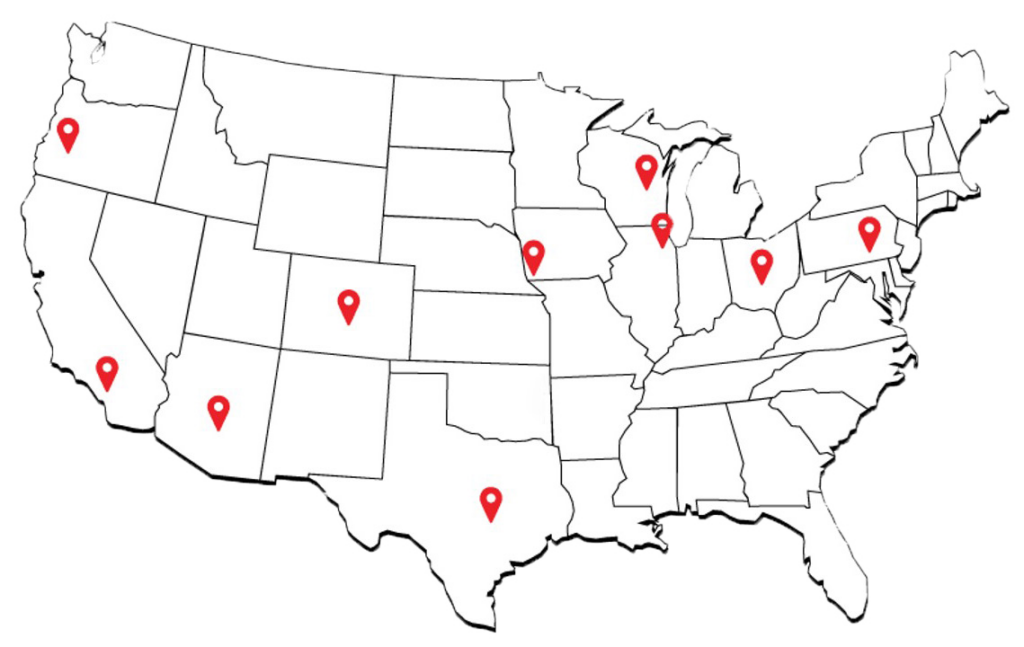
2,855,631 total square feet of chemical operations
Beyond traditional storage and handling, WSI performs minor blending operations involving totes and drums, as well as bulk transfers of liquids and dry materials. WSI manages rail-to-tanker and hopper trucks, rail-to-tank (storage), and rail-to-packaging transfers, ensuring seamless and contamination-free operations. WSI also conducts in-house transfers from super sacks to hopper trucks and provides freight brokerage to this customer.
Value Added Services
- blending
- sampling
- repackaging
- relabeling
- rebranding
- bulk transfers
- disposal
- spill mitigation
Finding Cost Efficiencies
The customer enjoyed measurable financial and operational benefits through WSI’s process improvements, established vendor relationships, and flexible financing options. By tapping into WSI’s vendor network, they secured better value on essential items, leading to notable cost savings.
WSI introduced a yard jockey trailer spotter, staffed by a licensed CDL driver, which streamlined logistics and eliminated the need for a dedicated vendor, thereby saving the customer time and money. Additionally, WSI’s flexible payment arrangements allowed the customer to manage their cash flow more effectively, freeing up resources for strategic investments.
A Shared Commitment to Environmental Stewardship
Over the years, the partnership between this plastics producer and WSI has grown, thanks to several key factors. First, WSI was able to seamlessly take over compliance audits and permitting responsibilities, which nurtured the customer’s trust in the 3PL’s capabilities.
Additionally, WSI’s commitment to responsible operations was demonstrated by becoming the first 3PL to achieve Responsible Care® Certification in 2013 and being named Partner of the Year. These accomplishments, combined with WSI’s proven track record of reliability, efficiency, and cost-effectiveness, solidified the customer’s confidence in the partnership, leading to its extension over decades.
In addition to continuous improvement of chemical handling practices, WSI also became a member of Operation Clean Sweep, an industry organization managed by the American Chemistry Council. This program is dedicated to eliminating plastic resin loss in operations, from manufacturing to warehousing to transportation. The purpose of membership is ensuring that resin is securely contained during these junctures in the value chain is critical to preventing loss into the environment and preserving water quality. The chemical producer’s commitment to excellence and sustainability aligned with WSI’s core values of safety, accountability, respect, and innovation.
A Partnership Built to Last
The partnership between WSI and this producer is a testament to the commitment to safety and innovative solutions in the chemical space. By working together, they have navigated complex logistics challenges, improving safety and efficiency, and driving sustainable growth. This enduring partnership serves as a model for successful collaboration, showcasing the benefits of a shared commitment to excellence.
Our commitment to safety and sustainability isn’t just about regulatory compliance; it’s how we demonstrate respect for our customers, employees, and the community.
Scott Buber | Director of Chemical Operations at WSI (Warehouse Specialists, LLC)
About WSI
WSI is a leading provider of third-party logistics services, delivering tailored solutions to meet the complex needs of its customers. The company’s expertise spans warehouse, labor management, e-commerce fulfillment, transportation management, and value-added services, including specialized handling, storage, and transportation of hazardous materials.