Safety Data Sheets: What Are They and Why They Matter
Hazard communication is one of the most frequently OSHA-cited warehouse worker safety issues. The consequences of inadequate communication can be severe, resulting in chemical burns, injuries, leaks, explosions, and fires, as well as insufficient medical care and prevention knowledge.
The key to mitigating these risks starts with maintaining a Safety Data Sheet (SDS) for each chemical that workers may be exposed to in the facility. These essential documents contain vital information about each chemical product, proper handling, storage, first aid, and spill resolution instructions.
Some companies, especially those handling small quantities or non-traditional chemical products, may not realize the need for Safety Data Sheets. Even everyday products can contain unexpected hazardous ingredients, making SDS management crucial for workplace safety and compliance.
In this article we look at what an SDS is, its importance in 3PL warehousing partnerships, the dangers of not having an SDS on file, and how to prepare an SDS if you don’t have one.
Let’s get started.
What is a Safety Data Sheet (SDS)?
A safety data sheet (SDS) is a document that provides essential information about chemical products as designated by the Occupational Safety and Health Administration (OSHA).
An SDS conveys detailed information such as “the properties of each chemical; the physical, health, and environmental health hazards; protective measures; and safety precautions for handling, storing, and transporting the chemical,” according to OSHA’s communication brief on SDSs.
OSHA also specifies that information contained in an SDS be in English and may also be in additional languages to ensure understanding and prevent potential language barrier issues.
OSHA requires 16 specific sections that must be included in each SDS document.
- Section 1: Product Identification
- Section 2: Hazard Identification
- Section 3: Composition/Information on Ingredients
- Section 4: First Aid Measures
- Section 5: Fire Fighting Measures
- Section 6: Accidental Release Measures
- Section 7: Handling and Storage
- Section 8: Exposure Controls and Personal Protection
- Section 9: Physical and Chemical Properties
- Section 10: Stability and Reactivity
- Section 11: Toxicological Information
- Section 12: Ecological Information
- Section 13: Disposal Considerations
- Section 14: Transport Information
- Section 15: Regulatory Information
- Section 16: Other Information
Go here to learn more about Chemical Warehousing OSHA Compliance & Regulations.
Why Are SDS Important to 3PL Partnerships
SDS are important to 3PL partnerships to ensure proper storage and handling of chemicals stored in their warehouses, to protect workers and communities from harm or injury, and to support responsible warehouse practices.
Ensuring Proper Storage and Handling
An SDS ensures proper storage and handling of chemicals in a warehouse by providing detailed instructions in section 7 about the safe handling and storage of the product.
For instance, some chemicals must maintain a certain distance from other substances, while others may require temperature or humidity control. Even the volume of a chemical that’s being stored can impact storage requirements.
Protecting Workers and Communities
OSHA requires that organizations provide in-depth chemical safety training for employees working with hazardous chemicals to learn how to protect themselves and others.
Organizations use SDS information to develop proper training for workers to ensure they understand the associated dangers, how to minimize risks, and respond to spills. This training goes beyond the SDS content by teaching employees the use of applicable PPEs, first aid, and steps in the event of leaks, fires, or explosions for optimum safety.
Proper SDS maintenance and training ensures compliance with OSHA regulations while supporting safer warehouse practices for employee and community well-being.
The EPA recently increased its chemical safety requirements for the Risk Management Program (RMP) to minimize community safety threats from leaks and explosions. The amended “Safer Communities by Chemical Accident Prevention Rule” requires greater prevention, preparedness, and public transparency. It is designed to protect communities near hazardous chemical storage and processing facilities from deaths, injuries, and property or environmental damage while preventing unnecessary evacuations.
The final rule improves chemical process safety, to help with planning, preparing for, and responding to incidents and is expected to reduce the frequency and severity of accidents. It’s important to know that 3PL partners, like WSI, who have already established a Responsible Care Management System were already meeting these more stringent requirements of this new EPA rule.
Responsible Warehousing Practices
Maintaining up-to-date SDS for all chemicals stored in 3PL warehouses is crucial to ensure proper storage, handling, training, and employee and community safety. However, top 3PL partners also practice responsible warehousing and participate in certification programs to foster safe chemical use, transport, and disposal.
For instance, partners who maintain Responsible Care (RC) certification through the American Chemistry Council have reduced recordable injury and illness rates by 20% since 2010. Those who participate in the Alliance for Chemical Distribution (ACD) Responsible Distribution program ensure chemicals are moved safely and responsibly.
Organizations like WSI participate in these programs and are committed to the practice and continuous improvement of environmental, health, and safety standards.

Potential Dangers of Not Having an SDS on File
Aside from violating OSHA regulations, there are numerous potential dangers associated with not having an SDS on file.
These dangers include:
Inadequate Response to Chemical Releases
In the event of a chemical release, such as an explosion or spill, not knowing the hazards can result in improper medical treatment. For instance, if a chemical is ingested versus merely contacting the skin, the first aid procedures differ significantly. An SDS provides the necessary information to care for injuries appropriately and prevent further reactions.
Improper Use of Personal Protective Equipment (PPE)
Not using the correct PPE during cleanup or handling can expose workers to hazardous substances, leading to health issues such as chemical burns, respiratory problems, or poisoning.
Environmental Risks
Improper handling and disposal of chemicals can cause significant environmental damage. Without an SDS, there’s a higher risk of contaminating water sources, soil, and air.
Fire Hazards
Different chemicals require specific methods for fire suppression. An SDS specifies whether to use foam, water, or other extinguishing agents.
Stability and Reactivity
An SDS provides information on chemical stability and potential reactivity with other substances.
Storage and Handling
An SDS outlines the necessary storage conditions, including ventilation, temperature control, and compatibility with other substances. The 2020 Beirut explosion is a tragic example of the dangers of improper storage and potentially not having an appropriate SDS on file. Thousands of tons of ammonium nitrate were stored improperly for years, leading to one of the largest non-nuclear explosions in history. This incident resulted in widespread devastation, loss of life, and severe damage to the city.
The Importance of Having SDS for 3PL RFPs
It’s essential to provide an SDS for each chemical to be stored at the time of the RFP. Doing so helps you avoid delays in the process, assess the potential partner’s commitment to safe and responsible practices, and develop the partnership.
Avoid Delays in the Process
Chemical products should be approved by a chemical or safety review team prior to storage inside a 3PL warehouse. Delays occur if an SDS is not available when the product is delivered to the warehouse. This means that the product cannot be unloaded into the warehouse and the load must be turned away until a compliant SDS is provided.
Assess 3PLs Commitment to Safety and Responsible Practices
Seek 3PLs who are Responsible Care Partners because they go above and beyond the standards that are set for the industry. Therefore, it is critical to provide a proper SDS to ensure your partner has the right infrastructure, equipment, and PPE in the warehouse to ensure the product is stored correctly and away from incompatible materials.
Demonstrate Compliance and Responsibility/Building Positive Partnerships
According to OSHA, an employer must maintain SDS copies for each hazardous chemical stored in their warehouse. Storing a product without an SDS not only risks a safety hazard, but it also puts the employer out of compliance with OSHA hazard communication standards. When an improper or no SDS is provided to the warehousing partner, it’s an opportunity to learn what a proper SDS looks like. Then your partner can guide you in the right direction to either obtain or prepare a proper SDS.
Obtaining and Managing Safety Data Sheets
Manufacturers, suppliers, or importers are typically responsible for creating SDSs, but companies must obtain and manage these critical documents. To obtain SDSs, companies can request them from their suppliers or manufacturers, check their websites for available documents, or utilize SDS management software to streamline the process.
Despite these measures, SDS management can be challenging, particularly for larger companies with complex operations. Managing multiple products and locations, maintaining extensive chemical inventories, and ensuring regulatory compliance can be overwhelming. Additionally, decentralization of SDS management across departments or locations can lead to inconsistencies and errors.
Some companies have dedicated teams to manage this, while others outsource SDS authoring and management to a vendor and utilize an SDS management software to ensure their data is organized, up-to-date, and well communicated.
Partner With a 3PL That Knows Chemical Storage
An SDS is an essential instrument for sharing hazard communication information to help keep warehouse employees safe. These documents contain vital information about each chemical product stored in a facility along with proper handling, storage, first aid, and spill resolution instructions.
These instruments are crucial to successful 3PL partnerships, enabling proper training, preparation, storage, and transportation for the safe storage of your chemicals. The information contained in an SDS makes it possible to protect workers and communities and support responsible warehousing practices.
When searching for a warehousing partner, seek a safety and sustainability-oriented 3PL that maintains RC certification through the ACC, participates in the ADC Responsible Distribution program, and submits to Ecovadis scoring like WSI.
When you partner with WSI, an SDS is the first thing we request from our clients to ensure safety and compliance. That’s our priority.
Contact us to learn more about partnering with WSI.

About the Author
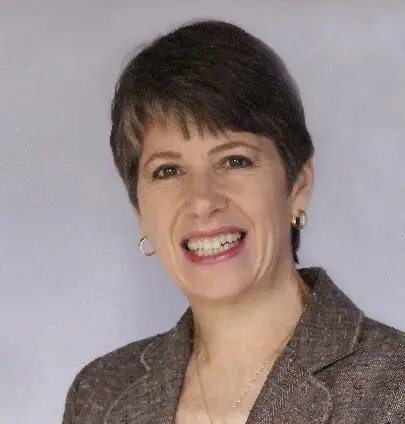
Margot Howard
Margot Howard is a Freelance content marketing writer and strategist with 10+ years of experience. Margot worked in corporate sales for many years before transitioning to content marketing. She writes for B2B SaaS, software, and service companies, especially those in shipping and logistics, Sales Tech, and MarTech.