Port to Warehouse Logistics: The Process
Have you ever wondered exactly how your freight gets from the port of entry to the warehouse? In the age of global sourcing, fuel, manufacturing widgets, furniture, clothing, and even food are traded all over the world. But with some global supply chains rethinking long shipping routes and favoring sourcing within North America, cross border trade continues to increase. With the introduction of new tariffs and associated regulations, restrictions, processes, and paperwork, businesses relying on the flow of goods to and from other continents find the journey from port to warehouse is more complex and costly.
As companies work through these international trade changes and learn to adapt to new realities, managing, monitoring, and moving cargo is under more scrutiny than before.
To understand how products ship from origin to port to warehouse to final destination, the following breaks down various transit modes to choose from.
From Port to Distribution Center
To track a container’s voyage from port to warehouse, the journey truly begins when products arrive via vessel, airplane, or train; and there are pros and cons to each.
Ocean Freight
In ocean shipping, freight containers are stacked onto carriers, then ferried across dedicated shipping lanes used for trade. Ocean freight is the most common transit mode–80% of cargo was moved by sea, though as supply chains continue to change and accommodate shorter regional routes, the numbers could adjust year to year.
Moving freight via an ocean container tends to be cheap relative to other options, but transit time can be slow. More recently, geopolitical stressors have added risks to ocean transport, impacting grain, cacao, and other dry bulk imports and exports. To maintain safety and efficiency, vessels have adjusted shipping routes around the Red Sea, avoiding high-risk areas near the Suez Canal. While these alternatives help ensure smooth transit, they also add costs and extend delivery times.
Security issues during transport are one of many dilemmas ocean carriers face. With wait times of more than six weeks from cargo load to destination port, unloading containers and moving product through customs adds even more time. U.S. CBP (Customs and Border Protection) workers need more time to use updated technologies, policies, and procedures, leaving merchants and consumers waiting longer for orders.
Extreme weather-related events like typhoons, hurricanes, and tornadoes can also slow ocean carrier shipping and docking times, as vessels may be forced to find other routes or wait out storms on calm waters.
Air Cargo
Shippers who do not have six weeks to wait might decide to use air freight delivery services. This mode moves freight by cargo plane or in the belly of a commercial plane. Fast and reliable, air freight typically has a heftier price tag compared to ocean shipping.
Air freight is often used to ship small, high value items with a short shelf life, like those sensitive to temperature swings, including pharmaceuticals or high value electronic parts. But with tariffs, new fees, and taxes proposed for 2025, some industries initiated a frontloading order surge to get ahead of long-term cost increases.
Rail
A boost in on-dock rail activity may be on the horizon due to tariffs, and an uptick in foreign and domestic businesses bringing manufacturing back into the U.S. And it’s no wonder.
Shipping rates can fluctuate, and fuel costs can skyrocket. For companies with a strong commitment to sustainability, rail serves long haul transport with a healthier carbon footprint. Rail is three to four times more fuel-efficient than trucks. One ton of freight moved by rail reduces greenhouse gas emissions by 75%, compared to hauling it by truck, and can move one ton of cargo more than 450 miles on a single gallon of fuel.

Port to Warehouse: Unloading Containers
Electing to ship goods by ocean, air, or rail is only the beginning.
The capacity of modern sea vessels is astounding. Depending on the length, width, and depth, a ULCS (Ultra Large Container Ship) could carry more than 24,000 containers. Once it reaches the port destination, the shipments are processed, unloaded, and moved to warehouses, distribution centers, or retail locations.
Port congestion can delay vessel arrival times and container releases. Once docked, it typically takes three days to unload, but as new trade regulations go into effect and customs officers get more familiar with the steps involved to process goods, container unloading cycle times will likely increase.
The Pacific Merchant Shipping Association’s 2024 Port Volumes Report showed the majority of North American ports increased container values from the year before. But even the largest ports can only handle so much freight—cranes, dock workers, and equipment are all in limited supply. As resources stretch thinner, and nearshoring and onshoring efforts rise, land transport could become a frontrunner.
Port to Warehouse: Land Transportation
Once freight is ready to head inland it needs to be hauled to its next destination by truck or rail. There are points to be considered before deciding on which transportation mode is best.
Trucking provides many options, giving 3PLs and their customers customized approaches. Depending on the circumstances, type of freight involved, and load size, a dry van, refrigerated trailer, or flatbed truck could work and require a whole trailer or only part of one.
Trucking brings a lot of flexibility. U.S. cross-border trade relies on trucking to move freight across North America: 66.5% of all surface trade with Canada, and 84.5% over the Mexican border in 2023.
Full Truckload (FTL)
First, there is the option to use a full truckload, referred to as FTL, giving the shipper the whole availability of the trailer. The kind of products hauled will dictate the type of truck needed; usually, it’s the standard 53-foot trailer, which can take 26 non-stackable pallets or 52 stackable ones.
A key benefit to FTL shipping is its speed. Though there is one point to be wary of: price. Reserving an entire truck could be worth it if the load is at full capacity; otherwise, unused storage space makes the haul more costly.
Less-Than Truckload (LTL)
When a freight order is smaller than the space of a whole truck, a less-than-truckload, or LTL, is ideal. This trucking option allows multiple shippers to share space on a truck and only pay for what they need.
While customers only pay for the space used, there are more stops during transit, making delivery times slower. Cargo risks increase; more stops mean more opportunities for mishandling products, theft, lost items, and mistakes in deliveries.
Intermodal with Rail
The true benefits of on-dock rail lie in cost-efficiency, sustainability, and productivity optimization. A typical rail yard can service multiple cargo containers, loading them directly onto rail cars. And with 41 million twenty-foot equivalent units (TEUs) expected to pass through ports of Long Beach and Los Angeles by 2040, moving cargo by rail can bring welcome relief to logistics providers and their customers.
Containers shipped by rail could require one or more stops across the country before the loads reach their final stop; and from there, they are loaded onto trucks until they reach their end delivery. The process is known as intermodal shipping because it uses multiple transportation modes to complete the journey.
But for businesses needing fast lead times or rapid order fulfillment to end-delivery, rail may not be the best option. Because trains move slower than trucks and have lengthier stops, rail tends to add a few days to the shipping journey, making arrival times hard to pinpoint.
For ecommerce businesses that need to move product from coast-to-coast, rail transit offers real savings that add up. Many online businesses and omnichannel retailers look to rail as a reliable shipping method which helps offset the increasing costs of last-mile delivery.
Selecting a Shipping Strategy
Moving products from port to warehouse can seem like a heavy lift. Knowing the options available and how to use them best can help make logistics decisions easier to navigate.
Optimizing routes and selecting the right transportation modes is easier when working with a 3PL provider that has a wide network of strategic logistics partnerships, warehousing facilities, and transloading locations.

About the Author
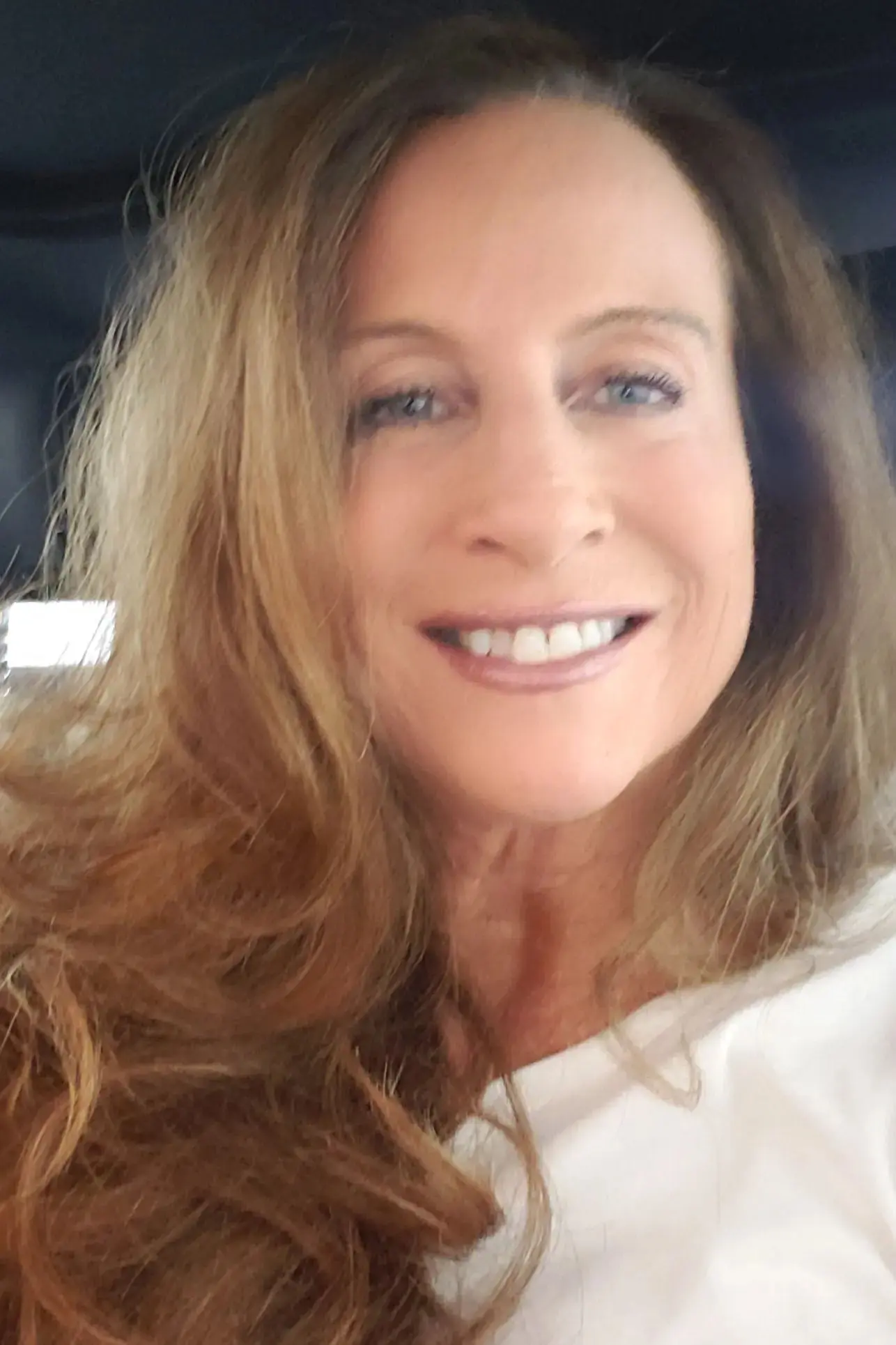
Melanie Stern
Melanie enjoys a longstanding career in communications, crafting content for varied industries. Her experience includes writing blogs, news editorial, feature articles, social, and broadcast segments. She also hosts Institute for Supply Management’s bi-weekly podcast “Supply Chain – Unfiltered”.