14 Most Common Warehouse Challenges
To those on the outside looking into the world of logistics, it might be hard to understand that warehousing is more complicated than it seems. After all, how difficult is it to put something on a shelf? Those who work in the industry understand that it takes hard work and know-how to do it right.
Far more than just a place to keep inventory, the modern warehouse is the heart of your supply chain. If you don’t do everything you can to keep it running efficiently and effectively, it could cause a domino effect that might leave you unable to fill orders the way your customers expect from you.
With that in mind, here are 10 of the most commonly found warehousing problems and solutions, so you can make sure your facility is working as well as it should be.
1. SUBOPTIMAL PICKING PATHS
Everything in your warehouse should be planned to make each process as smooth and effortless as possible. For example, the more territory your team has to cover to assemble an order, the longer each one takes to fill. This, of course, means that some orders that could be filled will have to wait until later, with the effect continuing to send shockwaves throughout your supply chain.
If you want to avoid this, the best course of action is to plan picking paths through your facility that minimize the number of steps each picker needs to take to get from one item to the next. It may require a little effort to help ensure proper groupings, but that’s nothing compared to the time you will be saving.
2. TOO MUCH INVENTORY
Keeping your shelves stocked with more inventory than you really need is one of the most challenging warehousing issues. Finding individual items becomes more challenging when shelf space is being used with products that don’t move fast enough, not to mention the safety hazards that cramped aisles can create in your busy working environment. It isn’t a matter of whether or not your stock brings you joy, but keeping your warehouse leaner can make you and your customers happier.
3. INEXPERIENCED AND UNDERTRAINED STAFF
Working in a warehouse is a physically demanding job at times, but that doesn’t mean it’s all brawn and no brain. Neglecting to keep staff fully trained and skimping on development opportunities is one of the biggest issues affecting warehousing today.
Many companies don’t prioritize training as much as they should due to budget concerns, they are setting themselves up for bigger losses down the road. Even if you need to hire some extra help to cover during these learning sessions, you will likely save a lot that would have been lost through mistakes and improper procedures.
4. IGNORING HEALTH AND SAFETY
Accidents on the job mean the potential for serious injuries — or worse. They also have the potential to significantly disrupt productivity. Unfortunately, far too many warehouses don’t give health and safety procedures the proper amount of attention and emphasis. Keeping aisles clear is important, but your employees also should be given all the tools they need to keep one another safe throughout the workday.
These include regular training and reminders as well as providing all the appropriate PPE. Reporting also should not be overlooked. When employees get in the habit of reporting any accidents or near-misses they encounter, you can gain a deeper understanding of where your protocols are working and where they need some improvement.
5. STICKING WITH ANTIQUATED PROCESSES
The most successful warehousing operations in the world today have a sophisticated data infrastructure humming behind the scenes. Tracking every item with barcode scanning, RFID tags, and other advanced processes helps ensure the information behind the goods moves along just as well as the shipments do. However, many companies still rely on old-fashioned pen-and-paper workflows to keep track of everything.
They may believe this saves them money, or keeps the complexity of their systems from getting out of hand, but the opposite is most likely true. Paperwork increases the risk of human error and adds to how long it takes to complete each individual task. Upgrading to a digital workflow may be a big initial investment, but it will pay off over the long run in a major way because it may help you avoid a large number of warehouse issues and problems.
6. FAILING TO KEEP CLEAN
Warehouses are industrial environments, and no one would expect them to be clean enough to eat off the floor. Yet that doesn’t mean you should ignore housekeeping duties each day.
Every piece of litter or clutter that takes space on your floor is a potential tripping hazard for your workers and slows work as everyone takes care to avoid them. This is why you simply can’t ignore the necessary tasks of keeping your facility neat and tidy at the end of every shift.
7. WORKING WITHOUT AN AUTOMATED SYSTEM
The modern warehouse is much too complex to manage entirely on your own. Having a warehouse management system software platform means much of the grunt work can be automated in the background while you and your team concentrate on more important jobs.
These systems will track your inventory levels, generate reports, manage labor, and other crucial tasks while you focus on other areas. Without automation, you can expect fulfillments to take more time and be at higher risk for mistakes and oversights.
8. IGNORING THE METRICS
You can’t hit a target if you have no idea where it is. This is why it is crucial for every warehousing operation to devote some of its energies to tracking key performance indicators (KPIs). Keeping a close eye on how well your team performs on a regular basis will show you where improvements need to be made and how you can eliminate pinch points.
This is another area in which having a robust warehouse management system can be extremely valuable. The regular reporting from your software makes it easy to see where you’re hitting the mark and where you need to adjust.
9. THINKING TOO SMALL
Your warehouse may be doing the job for you right now, but what about tomorrow? Are you ready if a sudden surge of orders comes in unexpectedly, or will you be swamped?
If your company is eyeing an expansion into a new market, for instance, the setup you have right now may not be adequate to handle it. The more prepared you are for what might come next, the easier it may be to roll with the changes and keep your momentum going.
10. TRYING TO DO IT ALL YOURSELF
There’s no shame in asking for help, especially when the future of your business is on the line. Finding a reputable and dependable third-party logistics (3PL) partner could be the difference between success and failure for you.
11. WAREHOUSE LAYOUT
In order to effectively run a warehouse, space is imperative. When appropriately utilized, warehouse layouts can help your team do more with the space they have available. From receiving areas to storage, operations managers need to have a well-planned outlayout for their warehouse. This will help eliminate wasted time walking back and forth through the warehouse and keep staff moving faster with designated space for each area of the warehouse. It seems like a pretty basic concept but you would be surprised how many warehouses aren’t laid out for smooth order fulfillment.
Solution: implement a warehouse management system to address your current warehouse layout and how it can be improved.
Most warehouse management systems use scanner technology, which provides data on the flow of goods throughout your warehouse. Managers can use this data to understand patterns in orders, areas of significant traffic, and the overall flow of storing and packing goods. This information can help redesign any areas within the warehouse that need to be reorganized.
12, INVENTORY TRACKING
It goes without saying but inventory is key to any successful business. Once a customer places an order, you must have the inventory to fulfill it. Mismanaged inventory, shortages, or delays in receiving inventory can significantly impact your bottom line. With the inevitability of human error and minimal transparency, manual tracking systems are becoming a strategy of the past.
Solution: use a cloud based warehouse management software to track inventory.
Enabling businesses to avoid many of the errors and issues that arise with traditional methods of measuring stock levels, cloud-based inventory management seamlessly keeps track of inventory coming in and going out of your business. These systems allow for more accurate and efficient inventory management and enable your staff to focus on more critical aspects of the business.
13. LABOR COSTS
According to a recent report, Labor Management Strategies in the Warehouse, 50 to 70% of a company’s warehousing budget is labor costs. Yes, you read that right. According to the study, labor comprises the largest portion of a warehouse’s total operating budget, making finding (and retaining) the right people and optimizing warehouse productivity a large priority.
It’s also important to address the additional costs that warehouses have endured due to COVID-19. From contactless order fulfillment, social distancing requirements, and regulated cleaning options, labor costs have significantly increased from the pre-pandemic budgets.
Solutions: implement a labor management system (LMS) that can reduce large labor forces and take over tedious, repetitive tasks.
Labor management systems are software applications that manage human resources within a distribution center operation. The LMS typically integrates with the warehouse management system. These systems feed data into the WMS to help reduce labor costs, predict labor shortages and drive productivity.
14. CUSTOMER SERVICE
In the end, it’s all about the customer. We have talked extensively about the Amazon effect and how customer expectations have shifted to create the need for fast and effective order fulfillment and delivery. Warehouse operations managers have to focus on customer satisfaction to drive revenue growth and build customer loyalty. This means that all touchpoints throughout the warehouse – picking, packing, shipping, delivery – are working together to deliver goods on time and accurately.
Solution: use warehouse management systems for transparency throughout the warehouse resulting in fast, reliable deliveries.
Warehouse management systems give operations managers the ability to track and evaluate the order process throughout their warehouse. These systems can recommend strategies and processes that need updating, take over time-consuming, repetitive tasks, and eradicate outdated practices.
TAKEAWAY
A 3PL company can provide you with the capacity and expertise so that your warehousing and other areas of the supply chain fit your needs as well as your customers’ needs.
As the recognized leaders in 3PL capabilities, WSI is your trusted resource to keep up with the speed of the marketplace. To learn more about what we have to offer you and your operations, get in touch today.
About the Author
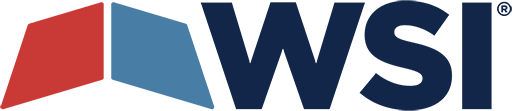
WSI Team
WSI is one of the largest privately held 3rd party logistics companies in the U.S. and spans a nationwide distribution network with global logistics reach.