Warehousing Building Materials Amid an Economic Boom
Building materials manufacturers, commercial developers, and construction companies are poised for a resurgence of activity. While many believe opportunities are waiting in the wings, inflation, interest rates, and consumer sentiment may continue to hold the cards toward growth or stagnation.
In the interim, businesses involved in these industries benefit from understanding what drives demand fluctuations and how to prepare for them. By warehousing building materials at various locations across the country, companies can serve localized, regional, and national markets throughout North America.
There’s a multi-step strategy behind it.
Let the Infrastructure Transformation Begin
Unknowns in changing government policies could affect environmental regulations and trade relations, impacting economic investments and the ways business leaders position their vision, mission, sourcing, and operations.
Transformation is no small feat—by definition, it’s a process.
Alex Darden, Partner at EQT Group, believes the U.S. is amid a decades-long infrastructure transformation, and the companies involved in the building and management of these projects will rely on strong fundamentals to navigate varied demand, cash flows, and pricing power.
The building materials industry plays a critical role in establishing readiness, response, and resiliency, expanding infrastructure and economic success.
Growth and Flexibility Meet Business Agility
Thanks, in part, to the U.S. bipartisan infrastructure law, increased funding for energy and transportation initiatives meant to bring people, business, and cross-border commerce together, come with roadblocks. Shifting regulations and monetary policies may escalate infrastructure development and associated costs, piercing budget ceilings.
The transit and storage of building materials are areas where increased efficiency and cost-savings can be captured. Massive projects, like the new Gordie Howe International Bridge, new railways in California, Nevada, and Washington, and Chicago’s O’Hare Airport expansion, require immense amounts of products to reach completion.
But the need for steel, concrete, composites, and other commodities doesn’t stop there.
Shaping the Urban Sprawl
Where commercial infrastructure goes, people and investments will follow, and often populate in tandem.
New housing starts support newly developed areas, giving people places to live while they work at jobs or open businesses near larger infrastructure projects. The urban expansion adds to the interconnectivity from city to city, state to state, and Canada through Mexico, reshaping supply chains into a wider regional net.
And because economies can quickly shift, procurement officers and supply chain professionals saddled with coordinating the purchase, transport, storage, and distribution of building materials carry a heavy load.
However, flexible warehousing solutions help manufacturers, suppliers, and retailers adapt to changing economic and population variables.

Warehousing Solutions for Building Materials
Building materials are the cornerstone of construction integrity affecting the versatility, value, and longevity of their application and end use.
Many of the construction materials builders rely on originate domestically or are sourced around the world. But it’s important to consider the differences in their makeup to ensure safe accessible storage wherever they sit.
For example, companies expecting to benefit from demand surges will want to store large building materials in bulk, in warehouses designed for that purpose. For sensitive or temperature-controlled storage, it’s important to ask if they have the capabilities to meet those requirements. Building materials tend to be heavy; without the right equipment and upskilled technicians, inflows and outflows can be challenging. Not to mention the specialized packing and loading called for.
Common building materials include:*
Steel – requires even temperatures for storage and shipping. Heat can cause unwanted expansion, warping the material, while cold could produce surface cracks, compromise durability, and use. Exposure to moisture can be problematic, affecting steel look and quality.
To protect steel in the warehouse and during shipping, use coatings or films on steel surfaces to reduce the risk of rusting. VCI wraps lessen the likelihood for corrosion, and keep steel in climate-controlled areas whenever possible.
Lumber – can be porous, and depending on the type of lumber, is more responsive to the elements. Wet and dry conditions, extreme temperatures, and poor air circulation lead to material rotting, warping, and cracking. When storing lumber, the area should contain stable temperatures and moderate humidity, best achieved in temperature-controlled spaces.
Stacking lumber is recommended, allowing for airflow on all sides of each board, and preventing mold. When stacking lumber, make sure the boards are flat, and begin stacking above floor-level on supports, with space between each board to allow air to flow freely. With every stack added, rotate the direction of the boards (by length and then by width).
Depending on what part of the country lumber is stored, materials can be relocated from inside the warehouse to outdoor storage, as long as temperatures and other weather conditions are moderate. For added protection, use tarp covering to ward off moisture exposure and leave a little give to keep airflow moving through it.
Aluminum – varying sizes and product weight provides opportunities in the warehouse to optimize aluminum’s storage capacity, by stacking lighter units on heavier ones. Much like steel and lumber, aluminum is better preserved in even-keel temperatures, away from moisture and harsh substances. Each piece is stored flat or on an edge, and separated by spaces consistently placed within every section. The sections are differentiated to minimize product cross-contamination.
Cement – has a time-sensitive nature, a powdery mix with a short shelf-to-use lifecycle. Storage areas need to be dry, with cement bags placed on boards or other surfaces above ground, and away from doors and windows.
Insulation – products, often mats or slabs, are highly sensitive to surrounding environments. The material can be adversely impacted by moisture, weather, and other products stored nearby. Safe storage includes lowering risk factors of product intrusion and increasing precautionary measures. Packaged insulation pallets are placed away from wet sources, heat, and direct sunlight, laid flat and horizontal or standing vertically, and stacked no more than three pallets high.
Composites – can take on what’s in the air around them. From dust, dry spatter from other materials stored, and food spillage, composites require tight-sealed containment in dry, steady conditions. Modifications in composite storage coincide with the type of material being stored. For example, fabrics can be damaged or altered by moisture or direct sun, affecting sizing and shape.

Where to Store Could Be a Multi-node Decision
Now that you know why building material demand is on the rise, and how storage plays a role in their safety and effectiveness, there are options in moving construction products to where they need to be.
New commercial infrastructure and master-planned communities cover large areas of land, with structures needing volumes of building materials, years before reaching completion. Developers and construction companies use many of the same purchasing principles found in other supply chains, where ordering in volume provides cost-savings and greater efficiencies. For their purposes, warehousing building materials makes sense.
Construction sites work through production phases, based on timelines dictated by permits, product availability, and sales. Having building materials readily available hel
ps keep to production deadlines as supply and demand shifts.
Exploring Rail-Served Warehouses
Building materials traditionally move in bulk, transported by ocean carrier to ports, and then broken down into smaller containers shipped in multiple trucks. The l
ogistics strategy can be overwhelming, and the more trucks required means more potential risk.
What about rail?
With pent up housing and commercial demand, rail transport could be the key differentiator for warehousing and transporting building materials.
By reducing reliance on trucks, businesses can move product and get closer to more sustainable carbon footprints. Less fuel use lowers overall emissions, and costs. But there’s more to rail than environmental benefits.
With rail, commodities like lumber, steel, and drywall, can be shipped farther and stored in more locations for added convenience and time-savings.
WSI has rail-served facilities across the country, streamlining and simplifying product transfers from railcars to storage in a single stop, reducing handling time and costs.
Inventory Management Strategies
Bringing multi-node operations into the fore of your storage and logistics needs helps ease the pressures of demand planning, and second-guessing whether just-in-time (JIT) or just-in-case (JIC) inventory methodologies is the answer.
With concurrent warehousing, intermodal, and transloading capabilities, inventory management can alternate between the two.
Product needs are subject to economic and geopolitical outliers beyond our control. And while business organizations seldom dictate these external events, how they ready for them and respond is where resiliency lives.
JIT inventory management
Real estate is typically a lagging indicator, steps behind current market trends. By reviewing historical data, manufacturers and suppliers are better equipped to anticipate building material inventories, and ensure they are in geographic locations providing the shortest routes to end customers.
The JIT inventory method gives businesses cost-saving opportunities by purchasing building materials as they are needed, tightening storage timelines, and supporting agile environments. But there’s room for JIC practices, too.
JIC inventory management
The last five years have shown that consumer confidence, fear, and public policies drive investments in commercial and residential real estate, with roller-coaster tendencies.
To prepare for the surg
es to come, keeping composite materials, steel, and lumber inventories at moderate levels could provide a healthy balance between meeting the needs of today and readying for tomorrow.
And by storing building supplies at inter-modal facilities, like WSI’s rail-served warehouse locations in California, Texas, Oregon, Arizona, Colorado, Pennsylvania, Illinois, and Wisconsin, businesses get the advantages of scalability and efficiency, minimizing shipment disruptions and saving costs transporting bulk building materials.
Simplifying Building Supply Transport
When it’s time to rev up new construction or support large-scale local revitalization projects, there are many moving parts to make it all happen on time with minimal hiccups. Partnering with an experienced 3PL provider offering a wide net of services, across multiple locations, gives construction industry decision-makers more tools in their toolbox.
WSI provides the best of logistics, warehouse and inventory management, and order fulfillment services available, and has been doing so since the 1960s. Strengthened by people, processes, and technologies, WSI boosts efficiency, visibility, and delivers reliability.
By upholding commitments to safe, ethical, and sustainable operations, storage, handling, and distribution of products come with peace of mind. WSI has the operational capabilities to warehouse building materials, and quickly pivot to distribution through rail and transloading facilities when the economy pushes forward.
*Building materials listed provide an overview. For details on specific product and storage requirements, refer to the product manufacturer for information.

About the Author
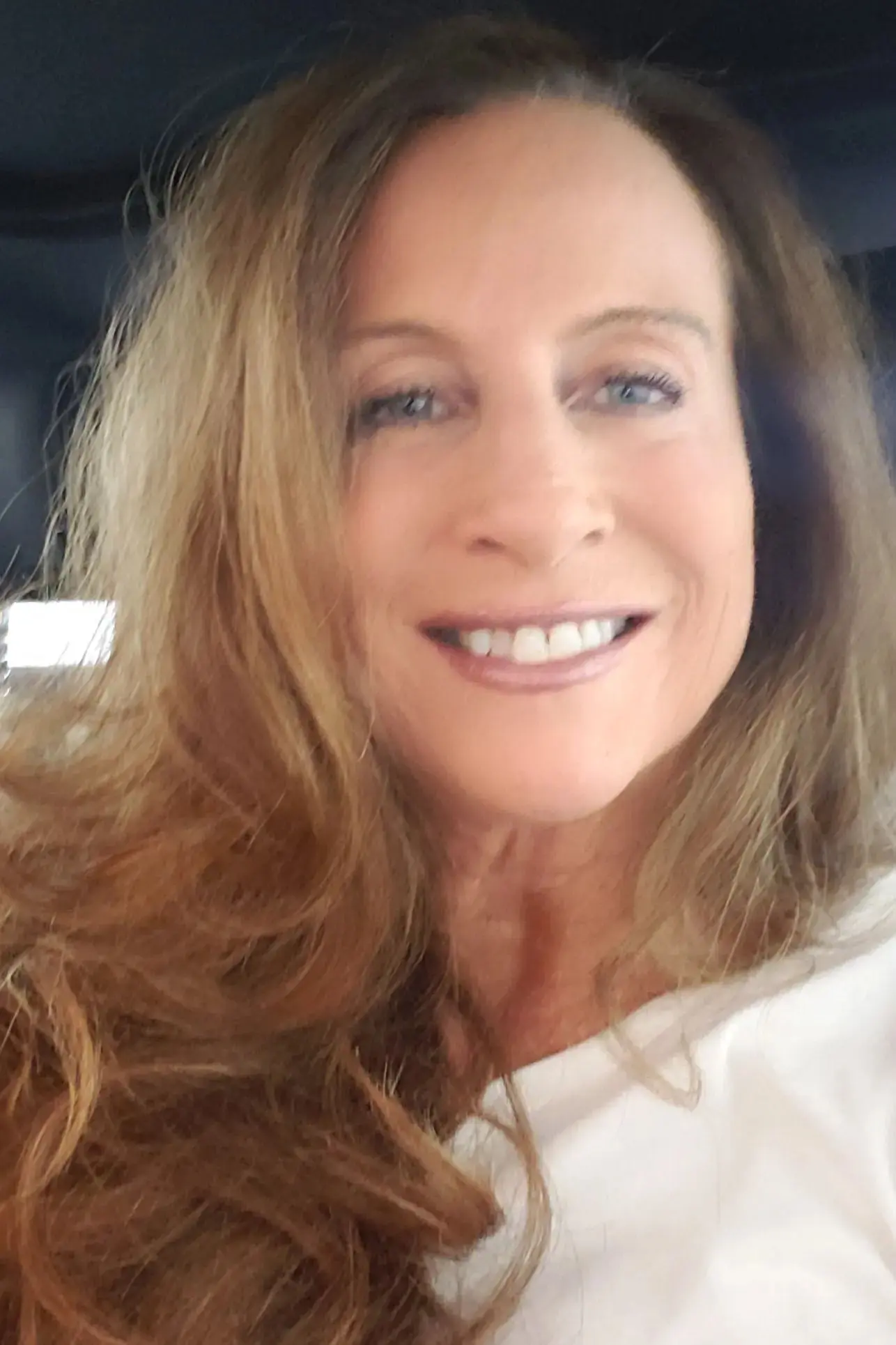
Melanie Stern
Melanie enjoys a longstanding career in communications, crafting content for varied industries. Her experience includes writing blogs, news editorial, feature articles, social, and broadcast segments. She also hosts Institute for Supply Management’s bi-weekly podcast “Supply Chain – Unfiltered”.